仕事でP板ドットコムに初めて注文を出した。
超お勧めなんで、ここに紹介キー貼っとく。よろしく。
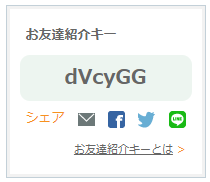
さて、それじゃ記事としてつまらんので経緯を話そう。
私の仕事はFA・・・ファクトリーオートメーションという分野で、電気制御を担当している。
凄く電子基板を扱いそうに聞こえるかもしれないけど、実際には全く使わない。
なぜなら、基本的にはPLCっていう市販のコントローラを中心に、モジュールになっているパーツを制御盤という箱にねじ止めして、それらを電線をネジで留めて組み立てて回路を作っているから。
というのも、電子基板っていうのはイニシャルコストという、「1枚作っても1万枚作っても一緒」というコストが掛かるので、作る枚数が少ないほど割高になってしまうのだ。なので、汎用のモジュールが発達していて、基本的に汎用のモジュールを組み合わせて、それにプログラムを書き込んでシステムが組めるようになっている・・・そんな世界なのだ。
ところが今回、物理的な大きさや電流的に要求されるパワーに制約があったりと、汎用部品で組み立てるととても大きくて収まらなくなってしまうような、微妙な電気仕様の装置だった。
回路的にはそう難しい回路では無いのだが・・・と悩んだ挙句、プリント基板を作ることにしたわけだ。
プリント基板とは
プリント基板とは、電気製品の中に入っている茶色とか緑の板のことだ。たぶん誰でも見たことがあると思う。
表に色々電気部品が付いていて、表面を模様のように電気回路が走っている奴。
なぜプリント基板と呼ぶのかというと、印刷に近い技法で製造されるから。
プリント基板が登場したのは1900年初頭とされ、それまでは複雑な回路も一本一本配線をしていた。全部の回路を一本ずつ配線していったのでは、スパゲッティのようにごちゃごちゃになるし、余った線の処理は大変だし、間違えるし、後からチェックしようにも大変である。(まぁ、制御盤なんかは未だに1本1本配線してて、これがまた大変なんだが・・・)
これを何とかしたいなーと考えた人が、「せや、板に電気が通るもので回路を書いたら、それが配線になるってのがエエヤン」と思いついたのが始まりか分からんけど、板に配線を描くことが考案された。
日本では1936年の「メタリコン吹き付け配線方法」特許がプリント基板の元祖とされている
この特許については私もあまり詳しくないのだが、基本的には配線の形に穴が開いた「テンプレート」を用意して、それを基盤に当てた状態で溶融亜鉛を吹き付け、後処理で定着させたようだ。
この溶融亜鉛を吹き付ける方法のことをメタリコン吹き付けというらしい。まぁ、孔版画をインクじゃなく溶融亜鉛でやったようなものだ。
このようにして一本一本配線を繋いでいく作業を、プリントという効率的な手法で置き換えていったのがプリント基板。
そして現代では製造方法はもうちょっと進んでいて、ウェットエッチング法が一般的である。
ロボコンでも散々作ったんだけど・・・ウェットエッチング法というのは、一面が銅張になった基板の要らない部分の銅箔を溶かす工法で製造するもの。版画とか美術的な技法で使われるあのエッチングと原理的には一緒。
版画とかでは原版を手で削って作るけれど、プリント基板の場合はもっと工業的だ。
まず、透明なフィルム上にプリントパターンを印刷したマスクというものを作る。
このマスクを感光基盤と呼ばれる基板に重ねて露光する。感光基盤というのは、全面に銅箔が貼ってあり、さらにその上に「フォトレジスト材」というのが塗ってあるものだ。フォトレジスト材は光に当たると変質するという特性を持っている薬品である。
つまり、マスクによって陰になったところは元のレジスト材が残っているが、陰にならなかったところのレジスト材は変質する。この状態でレジスト液というものに漬けると変質したところだけ溶け落ちて、その下の銅箔が露出する。これを現像という。
現像された基板を更に酸に漬けると、レジスト材が無い部分の銅が溶ける。最終的にマスクパターンの形に銅箔が残ることでプリント基板を成型する。
ロボコンではサンハヤトという基板メーカーの材料を使って、校内で内作していた。
メーカーの動画があった。
↓
作るのは結構大変
自作キットもあり、原理も単純なのだが・・・これが結構大変だ。
レジストパターンを綺麗に作るのも難しいし(プリンターのムラなんかで透けると、そこの配線が切れたりする)、露光もマスクがちょっとでも浮いていたりすると、光が回り込んで余計なところまでレジストが変性してしまう。つまりピンボケする。
また、エッチングもレジスト材がパターンを守ってはくれるのだが、側面方向は守ってくれないので、漬け込む時間を間違えると厚み方向から侵食されてパターンが細くなったり、切れてしまったりする。
エッチング液もレジスト液も使っていくうちに純度が落ちていくから、性能も変わってきて、漬け込み時間なんかも調整せねばならず、実は結構難しいのだ・・・
ロボコンでは1枚の基盤を作るのに、2枚も3枚も無駄にしたりというのはザラだった。基盤が大きくて、配線が細かいほど難しくなる。
さらに地獄の後工程があって、部品の足が刺さる穴をドリルで一つ一つ開けていかねばならない・・・エッチングでは穴はあかないからだ。
孔も0.3mmとか滅茶苦茶細いから、高速ドリル+趙堅ビットで開けていく。
で、プリント基板を作るのはそれだけ大変なので、実はそういう専用の機械がある。
自動でレジストして、自動で露光して、穴あけから部品取り付けまで自動でやる装置である。数百万円から買えるので、前の会社にはそういう装置を置いた部署があった。
ただ、今の勤務先には無いし、仮に買ってもらったとしても素人がパッと使えるようなものじゃない。
外注が便利
というわけで、今回はP板ドットコムを利用してみた。
P板ドットコムというのは、私がロボコンをしていたころからあった。確か何枚か出したことはあった。
その後、最初に就職した会社は基板製造チームがあったので、社会人になってからは一度も外注していない。
そして月日が流れ・・・例の「汎用パーツで組むと大きくなりすぎる装置」の開発で悩んでいた。
パッと「よし、基板を作ろう」となればよかったのだが、長いこと基盤から離れていたし、もともとは汎用のパーツでそれなりにコンパクトに収まる仕様だった。ただ、開発の進行に伴って機械的な性能の問題からパーツ変更が生じたり、大きさの制約がタイトになったりと、だんだんニッチモサッチもいかなくなっていったのだ。
そんな中ある休日に妻の実家に行ってお茶をしていたら・・・キッチンに乱雑に積まれた入れ物になっている箱の中の一つに、「P板ドットコム」と印刷された箱が目に留まった。
義父は研究者だから、何か実験の都合で基盤を頼んだのだろう。
「P板ドットコム」ってまだあったのか・・・と思ったら、かなり大きい会社に成長していて、値段も滅茶苦茶高かったイメージから、かなり安くなっていた。
今回作ってもらった基盤は20cm×10cmの中くらいのもので、10枚製造して3万円ほどだった。
まぁ、ロボコンの部品としては高価な部類だが・・・企業の研究開発部材としてはコピー用紙とそう変わらない価格帯である。
という訳で使い始めたわけだ。
基板起こして正解だった
正直、今の勤務先では例がない取り組みだったからリスクもあった。基本的に設計というのは設計者と別に検図者がチェックをするものだが、会社にはプリント基板のチェックどころか、電子回路が分かる人間すら居ない。
意外かもしれないが、制御盤を中心とした電気設計と、基板を設計する能力とでは、例えば医者でいうとないかでも脳神経内科と消化器内科くらい違う…と思う。
設計通り動くかどうか凄く心配だったけれど、組立てテストしたら設計通り動いた。まぁ、動くように設計して、いろんなチェックを経て製造したわけだから、当たり前だけど・・・。
お蔭でまた「できっこない」と言う輩にドヤることができた。
それに基板だからこそできるちょっとした機能なんかをいくつか付けたんだけど、これが結構良くってなんか付加機能/特許に発展しそうな感じもある。
やっぱり挑戦だよねと思った今日この頃だ。